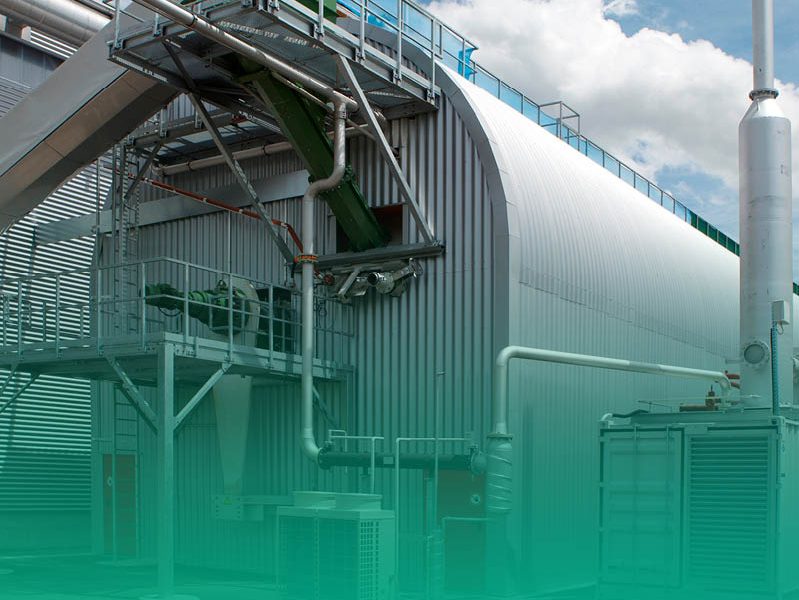
Ci spiace, ma questo articolo è disponibile soltanto in English e Deutsch. Per ragioni di convenienza del visitatore, il contenuto è mostrato sotto nella lingua principale di questo sito. Puoi cliccare su uno dei links per cambiare la lingua del sito in un’altra lingua disponibile.
In the age of the circular economy, ways of recycling and recovering organic waste as a renewable, natural resource are attracting increasing attention. Kanadevia Inova’s Kompogas® process uses continuous anaerobic digestion to recycle biogenic waste, producing natural fertiliser and renewable energy in the form of green power and heat or biogas as the basis for alternative fuels. By recycling organic waste into materials and energy, the process closes the environmental cycle cost-efficiently.
Thanks to its robust, modular design, the Kompogas® technology has become one of the global market leaders, with almost 100 reference plants worldwide. Mature technology, flexible component arrangements and largely automated processes guarantee long plant lifetimes, high efficiency and low maintenance costs.
Depending on local waste management arrangements, organic waste can include kitchen waste as well as municipal and commercial green waste. With such waste mixtures, which typically contain high proportions of solids and foreign matter, the advantages of dry anaerobic digestion come into their own. A distinction is made between two types of waste fraction:
Both material flows produce a high-grade renewable fuel in the form of biogas.
One tonne of organic waste yields:
This biogas can be treated in a gas upgrading plant to produce approximately 60 Nm3 of biomethane and converted into compressed or liquid biogas, a carbon-neutral fuel replacing about 60 litres of diesel. The biomethane can also be fed into the existing gas grid, making an important contribution to decarbonisation.
Alternatively the biogas can be converted into around 250 kWh of green electricity, plus at least the same amount of heat, in a combined heat and power unit.
This way, Kompogas® technology closes both the materials and energy cycles.
Depending on local waste management arrangements, organic waste can include kitchen waste as well as municipal and commercial green waste. With such waste mixtures, which typically contain high proportions of solids and foreign matter, the advantages of dry anaerobic digestion come into their own. A distinction is made between two types of waste fraction:
Both material flows produce a high-grade renewable fuel in the form of biogas.
One tonne of organic waste yields:
This biogas can be treated in a gas upgrading plant to produce approximately 60 Nm3of biomethane and converted into compressed or liquid biogas, a carbon-neutral fuel replacing about 60 litres of diesel. The biomethane can also be fed into the existing gas grid, making an important contribution to decarbonisation.
Alternatively the biogas can be converted into around 250 kWh of green electricity, plus at least the same amount of heat, in a combined heat and power unit.
This way, Kompogas® technology closes both the materials and energy cycles.
Media error: Format(s) not supported or source(s) not found
Scarica il file: https://www.kanadevia-inova.com/wp-content/uploads/2020/06/kompogas-introduction.mp4?_=1Kompogas® technology from Kanadevia Inova uses continuous dry anaerobic digestion to treat organic waste and convert it into new products.
Waste is received in either a deep bunker or tipping area with an odour trap. The fully automated crane system transports the waste from the bunker to the shredder where the organic material is shredded and sieved. The fraction in the >60mm range is returned to the bunker, while a conveyor system takes the sieved-out substrate to the digester.
The core module of every Kompogas® plant is the digester. Material fed into the digester is digested by thermophilic microorganisms at a temperature of 55°C under anaerobic conditions. The substrate moves steadily and horizontally forward through the plug-flow digester as digestion proceeds, producing biogas in the process. Fresh material is constantly fed in, with part of the recirculate from the digestate added to inoculate it and immediately activate the digestion process. Retaining the substrate for around 14 days at this temperature makes sure that it is completely sanitised and its gas potential fully exploited.
Once the retention time has elapsed, the digested substrate is pumped out at the discharge outlet of the digester. The Kanadevia Inova Kom+Press dewatering press separates it into a solid and a liquid fraction. After a short post-treatment phase, the solid digestate is ready for use as a raw organic fertiliser and soil conditioner, or for further processing to produce high-grade compost. Where there are no regulations to the contrary, the liquid digestate is also used in agriculture. If necessary, the dry matter content is reduced even further using the Kanadevia Inova SpeedScreen.
In cases where the use of liquid fertiliser is prohibited, the liquid fraction is either passed into a waste water purification system or used for presswater-free partial stream anaerobic digestion. In the latter case only the energy-rich component of the biowaste is fed into the digester. The highly structured material is shredded, and only mixed into the digestate after the digestion process. This completely eliminates the need for dewatering. Then the material undergoes aerobic composting.
The Kompogas® plant is designed as an enclosed system to prevent the emission of odours. During the process, the exhaust air is gradually collected and pre-cleaned in an acid scrubber. Then it passes through a biofilter made of torn root wood and tree bark before being released into the atmosphere practically odour-free.
The raw biogas produced in the digestion process is either upgraded to biomethane using Kanadevia Inova’s BioMethan technology and fed into the grid, or further treated (compressed or liquefied) to produce high-grade fuel. Alternatively, the raw biogas can be used to generate carbon-neutral electricity and heat in a combined heat and power (CHP) unit. In this case a small portion of the heat is used to maintain the temperature in the digester, with the rest used in buildings close by or fed into the district heating network.
Waste is received in either a deep bunker or tipping area with an odour trap. The fully automated crane system transports the waste from the bunker to the shredder where the organic material is shredded and sieved. The fraction in the >60mm range is returned to the bunker, while a conveyor system takes the sieved-out substrate to the digester.
Once the retention time has elapsed, the digested substrate is pumped out at the discharge outlet of the digester. The Kanadevia Inova Kom+Press dewatering press separates it into a solid and a liquid fraction. After a short post-treatment phase, the solid digestate is ready for use as a raw organic fertiliser and soil conditioner, or for further processing to produce high-grade compost. Where there are no regulations to the contrary, the liquid digestate is also used in agriculture. If necessary, the dry matter content is reduced even further using the Kanadevia Inova SpeedScreen.
In cases where the use of liquid fertiliser is prohibited, the liquid fraction is either passed into a waste water purification system or used for presswater-free partial stream anaerobic digestion. In the latter case only the energy-rich component of the biowaste is fed into the digester. The highly structured material is shredded, and only mixed into the digestate after the digestion process. This completely eliminates the need for dewatering. Then the material undergoes aerobic composting.
The Kompogas® plant is designed as an enclosed system to prevent the emission of odours. During the process, the exhaust air is gradually collected and pre-cleaned in an acid scrubber. Then it passes through a biofilter made of torn root wood and tree bark before being released into the atmosphere practically odour-free.
The raw biogas produced in the digestion process is either upgraded to biomethane using Kanadevia Inova’s BioMethan technology and fed into the grid, or further treated (compressed or liquefied) to produce high-grade fuel. Alternatively, the raw biogas can be used to generate carbon-neutral electricity and heat in a combined heat and power (CHP) unit. In this case a small portion of the heat is used to maintain the temperature in the digester, with the rest used in buildings close by or fed into the district heating network.
Kanadevia Inova designs, builds and operates biogas plants featuring its proven Kompogas® dry anaerobic digestion technology all over the world. The benefits:
Visit our Kompogas® plant in Jönköping virtually:
The heart of every Kompogas® plant is the horizontal plug-flow digester. It is available in modular construction, in either steel or concrete, in a range of sizes from a usable volume of 1,200 m3. The streamlined design of both types facilitates space-saving arrangements. Several digesters can be combined and operated in parallel for plants with a large throughput.
Both types meet the stringent water pollution regulations in different countries. The horizontal agitator is structurally designed to withstand very high torque loads and enable smooth restarts after periods of downtime. A plough-shaped paddlehead ensures that the substrate is optimally mixed and degassed. This prevents excessive sedimentation of solids in the digester and thus allows many years of operation without interruption for maintenance.
A built-in heating system facilitates the thermophilic process and makes sure that the digestate is completely sanitised, while a specially developed inoculation system ensures a stable biological process.
Visit our Kompogas® digester in Jönköping virtually:
The Kom+Press is a high-performance, high-precision dewatering press for separating solid and liquid digestate. It features a screw with bearings on both sides and hard-faced polished spiral coils. Together with a shorter head, the adapted construction of the wear parts in the inlet shaft and high-end wear plates at the relevant points, this prolongs the lifetime of the unit.
Thanks to a manual swing-up basket and sieve, a single person can change the sieve without removing the basket, enabling heavily stressed sieves and wear parts to be changed quickly and easily. The functional design facilitates access and cleaning, which also reduces the costs of maintenance.
Visit our Kom+Press unit in Jönköping virtually:
The Kanadevia Inova SpeedScreen was developed to allow 24/7 operation by removing solids such as sand and organic fibres from liquid digestate. Intelligent design and efficient rotation eliminate the need for flocking agent or rinsing water and enhance the quality of the filter cake. The screen baskets, available in different mesh sizes, are very easy to swap out, keeping operating and maintenance costs low.
The people at the Kanadevia Inova Service Group support plants through their entire life cycle. Our service portfolio ranges from delivering spare parts through to extensive retrofits.
Clients profit from Kanadevia Inova’s wealth of experience in the service business and project delivery, comprehensive technological know-how, and a wide range of tried-and-tested components manufactured in-house. Geographic proximity to our clients’ plants guarantees a rapid response and bespoke services.
Thanks to artificial intelligence, the automated early detection of disturbances in the biological process in the digester is possible within a few seconds. In the event of a disturbance, the system triggers an alarm and enables the operating personnel to intervene as quickly as possible. The system uses plant data available online from existing measurements, meaning that it can be used in many different types of plant.
Conventional laboratory analysis is no longer necessary and the continuous monitoring of the biological process in real time eliminates the delay before a malfunction is detected. Detection happens within seconds rather than days.