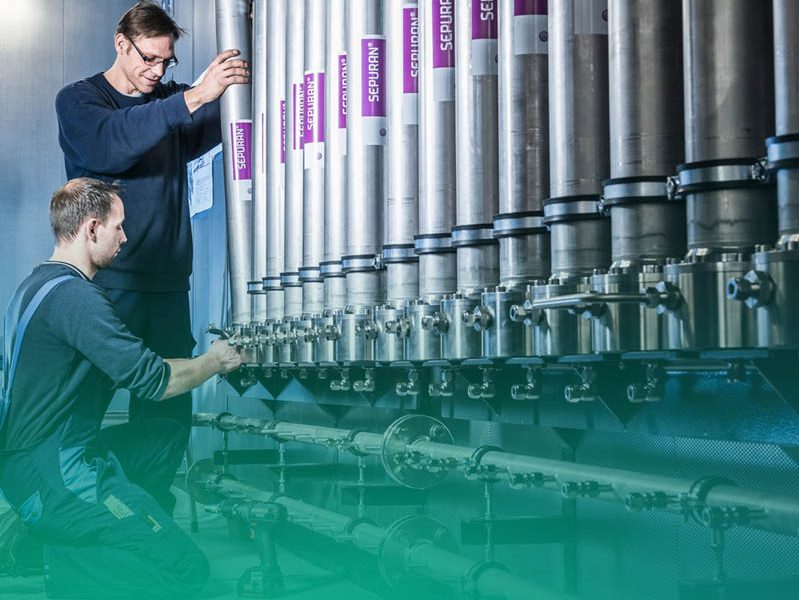
Our Service Offering
Your plant is in the best possible hands. Kanadevia Inova’s Service Group is there to support you with outstanding service around your WtE or renewable gas installation. Our work is always geared to four overarching goals:
Our experts can provide quality training either on site or remotely. Trainings are adapted to the specific needs of the client and provided by experienced experts in the relevant field. Contact us. We’ll be glad to put together a programme of practical training tailored to your individual requirements.
To maximise plant availability it’s important to have a dependable supply of the necessary spare parts. We take care of this for you, delivering promptly and reliably.
Our supply chain for spare and wear parts deliberately relies on a high proportion of European suppliers. We have our own workshop and integrated warehouse in Buchs, Canton St Gallen (Switzerland), to enable the manufacture of parts to specific client requirements and efficient, no-nonsense logistics. This minimises response times and enables us to deliver quickly and reliably in the event of disruption. Alternatively we can also offer on-site container solutions to meet your spare and wear parts needs.
Our core business is improving and enhancing your plant. To analyse your individual requirements, we guide and support you through the entire process, from inspecting your plant to doing the economic analysis. Our services span:
Thanks to decades of experience in the service business and cooperation with specialists in various areas of technical expertise, we are able to rapidly identify issues and find sustainable, cost-efficient solutions. Talk to us, no strings attached.
Our team of specialists will take care of planning service and installation work on your behalf and then execute expertly and reliably. Customised service agreements give you precisely the services you need to add the desired value. Our services include:
Overhauls:
Executing installation work:
With almost a century of experience in plant engineering, we have a profound understanding of the systems and processes involved in WtE and biogas installations. Our service teams will execute your conversion or retrofit project expertly and efficiently on an integrated basis, providing the entire service, from concept to commissioning, on a one-stop basis.
We can replace or modernise specific components and subsystems, always with a view to the goals defined by the client:
Our lab has been an integral part of our business for more than 70 years. Equipped with the latest measurement technology, it enables us to offer the WtE and biogas industries a broad range of analysis and evaluation services.
We verify compliance with emission limits and performance guarantees, measure the relevant process parameters, and support you in solving process-related issues.
Our lab offers:
We’re a reliable partner with the expertise to guide and support your lot project. Thanks to comprehensive plant engineering know-how, we’re able to swap out existing subsystems or extend your plant for improved profitability.
Our Service Offering
Your plant is in the best possible hands. Kanadevia Inova’s Service Group is there to support you with outstanding service around your WtE or renewable gas installation. Our work is always geared to four overarching goals:
Our experts can provide quality training either on site or remotely. Trainings are adapted to the specific needs of the client and provided by experienced experts in the relevant field. Contact us. We’ll be glad to put together a programme of practical training tailored to your individual requirements.
To maximise plant availability it’s important to have a dependable supply of the necessary spare parts. We take care of this for you, delivering promptly and reliably.
Our supply chain for spare and wear parts deliberately relies on a high proportion of European suppliers. We have our own workshop and integrated warehouse in Buchs, Canton St Gallen (Switzerland), to enable the manufacture of parts to specific client requirements and efficient, no-nonsense logistics. This minimises response times and enables us to deliver quickly and reliably in the event of disruption. Alternatively we can also offer on-site container solutions to meet your spare and wear parts needs.
Our core business is improving and enhancing your plant. To analyse your individual requirements, we guide and support you through the entire process, from inspecting your plant to doing the economic analysis. Our services span:
Thanks to decades of experience in the service business and cooperation with specialists in various areas of technical expertise, we are able to rapidly identify issues and find sustainable, cost-efficient solutions. Talk to us, no strings attached.
Our team of specialists will take care of planning service and installation work on your behalf and then execute expertly and reliably. Customised service agreements give you precisely the services you need to add the desired value. Our services include:
Overhauls:
Executing installation work:
With almost a century of experience in plant engineering, we have a profound understanding of the systems and processes involved in WtE and biogas installations. Our service teams will execute your conversion or retrofit project expertly and efficiently on an integrated basis, providing the entire service, from concept to commissioning, on a one-stop basis.
We can replace or modernise specific components and subsystems, always with a view to the goals defined by the client:
Our lab has been an integral part of our business for more than 70 years. Equipped with the latest measurement technology, it enables us to offer the WtE and biogas industries a broad range of analysis and evaluation services.
We verify compliance with emission limits and performance guarantees, measure the relevant process parameters, and support you in solving process-related issues.
Our lab offers:
We’re a reliable partner with the expertise to guide and support your lot project. Thanks to comprehensive plant engineering know-how, we’re able to swap out existing subsystems or extend your plant for improved profitability.
Find the right solutions and services for your plant. Our modules can also be built into existing plants from other providers.
Kanadevia Inova Feed Hopper
The Kanadevia Inova Feed Hopper consists of individual water-cooled modules. The interior surfaces are made of wear-resistant materials to withstand heavy use. Depending on the position of the individual modules and the stresses to which they are subject, they are made of different materials and can be repaired or replaced independently of each other. The Kanadevia Inova feed hopper is incorporated in the existing steel structure, adapted in line with the specific circumstances. This makes it the ideal retrofit for a range of WtE plants.
References: Zorbau, Zisterdorf, Umea
Download: Kanadevia Inova Feed Hopper Brochure
Inova Grate
The new Inova Grate is a reciprocating grate with physically separated grate zones and individual reciprocating grate elements. The grate is built to be inclined at a lower angle, allowing a lower and more compact design and reducing the space required. At the same time larger grate blocks enable the subsequent costs of operation to be reduced. The size of the grate and the appropriate cooling system (water or air) are determined on the basis of the combustion diagram and the specific requirements of the plant and the waste processed.
References for Inova Grate: Lucerne, Poznan, Ivry*, Rockingham*
*Under construction
Kanadevia Inova R-Series Grate
The R-Series incinerator grate developed in-house by Kanadevia Inova is a reciprocating grate inclined at an angle of 18° with individually movable grate elements. This feature enables operational flexibility and ensures that the waste is transported, mixed and combusted efficiently. The R-series grate is air-cooled as standard. The size of the grate is determined on the basis of the requirements specific to the plant and the waste it treats.
References: Cleveland 3, 4 & 5, Riverside, Newhaven, Jabalpur, Severnside, Dublin, Edinburgh, Moscow 1*
*Under construction
Grate Cooling
All our grates can be built with water or air cooling, with the choice depending on the combustion diagram and the specific requirements of the plant and the waste processed. Air cooling makes sense if the calorific value of the waste is low to average. Here the primary air is also used to cool the grate. For waste with a higher calorific value a water-cooled grate makes more sense. By decoupling grate cooling from the air supply, the air supply also enhances the combustion process, resulting in better quality bottom ash and less flue gas.
References for air cooling: East Rockingham*, Newhurst*, Rookery*, Moscow 1*, Istanbul*, Edinburgh, Dublin, H&W, Poznan, Severnside, Jabalpur, Buckinghamshire
References for water cooling: Ivry-sur-Seine*, Ferrybridge 1 + 2, Horgen, Lucerne, Vantaa, Vasaa, Oslo
Low Excess Air Process (LEAP)
Our staged combustion process consists of two injection stages for secondary air and recirculated flue gas. LEAP reduces the combustion air flow rate in your installation, enabling the use of smaller components for the boiler and flue gas treatment system. Even distribution of corrosive agents thanks to intense mixing also reduces the risk that the boiler will corrode, even at lower oxygen levels.
References with flue gas circulation: Lucerne, Dublin, Oslo, Lausanne
References without flue gas circulation: Vaasa, Horgen
Download: LEAP brochure
Boiler
We design and build custom boilers, both horizontal and vertical. Our compact design enables us to make the best possible use of the space available and optimise the flow of exhaust gases even if space is limited.
References for horizontal boiler passes: Moscow*, Istanbul*, Ferrybridge I+II, Edinburgh, Hereford & Worcestershire, Dublin
References for vertical boiler passes: Jabalpur, Cleveland 4&5, Poznan, Bamberg, Barcelona, Pithiviers, Stassfurt, Cleveland 3
*Under construction
Kanadevia Inova Primary Air Filter
Primary air is sucked out of the waste bunker to prevent emissions of dust and odors into the environment. The primary air filter cleans this air so that the primary air preheater becomes dirty less quickly. This avoids the need for cleaning services and allows the plant to run continuously for longer.
References: Thun
Monitoring the Boiler Rapper System
Kanadevia Inova’s boiler rapping monitoring system checks the functional integrity of the rapper during operation. If the function of a harp is found to be limited, the system automatically increases the rapping force and adjusts the rapping frequency while simultaneously alerting the operator. The online monitoring tool is suitable for both mechanical and pneumatic rappers.
Download: Online Boiler Rapper Brochure
DyNOR®: Kanadevia Inova’s Advanced SNCR Process
The DyNOR® system developed by Kanadevia Inova’s engineers is an improved selective non-catalytic reduction (SNCR process). It enables nitrogen oxide to be reduced to very low levels with minimal ammonia slip, something that was previously only possible with an SCR (selective catalytic reduction) process. The non-catalytic DyNOR® process closes the gap between the costly SCR process and the conventional SNCR process.
References: Vaasa, Vantaa, Severnside, Dublin, Poznan
Download: Brochure Dynor SNCR Process
Dry Sorption: XeroSorp Bicar/Lime
Dry sorption involves neutralising acid gases by with neutralising additives, but without water. In our XeroSorp process we use hydrated lime of sodium hydrogen carbonate (sodium bicarbonate). The system is outstanding in terms of low investment and operating costs, and requires little space in your installation.
References: Bellegarde*, Istanbul*, Edinburg, Lucerne, Horgen, Issy-les-Moulineaux
Semidry Sorption Process (Kanadevia Inova SemiDry)
The Kanadevia Inova SemiDry system involves a semidry sorption process employing the principle of the circulating fluidised bed. Hydrated lime and water are injected in to neutralise acid gases. The system is a highly effective means of reducing emissions and is very flexible in terms of a range of process factors. This all makes it very popular in the industry.
References: Dublin, Ferrybridge 1+2, Hereford and Bedfordshire, Poznan, Severnside, Buckinghamshire, Cleveland
Kanadevia Inova Pulse Jet Monitoring
Kanadevia Inova’s pulse jet monitoring system monitors and controls the cleaning of the filter chambers. It uses the measurement data gathered as the basis for coordinating the selective cleaning of filter bags and regulates cleaning sequences for individual filter bag lines. Thanks to high-performance sensors, the automated control system to instantly detects valve failures and damage to bags, and displays the position and type of defect for the operator.
Wet Scrubbing Kanadevia Inova WetScrubber
Wet scrubbing is the most effective method for removing acid gases from even heavily burdened flue gases, achieving the lowest emissions. The process is also excellent for removing fine particulate and aerosols. The Kanadevia Inova WetScrubber consists of multiple stages that can be combined on a variable basis to tailor the process individually to the client’s requirements.
References: Dublin, Oslo, Trondheim, Lausanne
Download: Brochure Oxi-Air – Wet Scrubbing
Kanadevia Inova RingJet
The ringjet stage is a very typical component of wet scrubbing. Placed in the scrubber, Kanadevia Inova RingJets produce a mist of water that separates fine particulates and aerosols from the exhaust air or flue gases. Laden with pollutants, the droplets are then removed. The Kanadevia Inova RingJet is easy to fit, robust and to a large extent maintenance-free. It is space-saving, and can also be retrofitted to existing scrubbing towers.
References: Buchs, Oslo, Trondheim, Limmattal, Lausanne
Download: Brochure Kanadevia Inova RingJet
Kanadevia Inova CondensingScrubber
In addition to the benefits of the Kanadevia Inova WetScrubber, the Kanadevia Inova CondensingScrubber allows heat to be recovered by condensing the water vapour contained in the flue gas. This way a plant can achieve overall energy efficiency of more than 100%.
References: Oslo
DeNOx Systems
We use different SCR (selective catalytic reduction) and SNCR (selective non-catalytic reduction) systems to remove the nitrogen oxides produced in the combustion process.
Kanadevia Inova DryMining
Kanadevia Inova DryMining is a fully automatic treatment process for recovering ferrous and nonferrous metals from bottom ash and the boiler ash. The tower installation can be used with wet or dry fine bottom ash discharge. The first step is to separate out the ferrous metals, before the nonferrous metals are sieved out and sorted by density. The process is controlled either from the control tower or with the help of a local switchboard.
References: Horgen, Emmenspitz
Download: Brochure InovaRe
Grate for Riddlings
Around 70% of valuable nonferrous metals are to be found in the <10 mm fine fraction of the bottom ash. Our Grate for Riddlings is geared to recovering this fine fraction. It contains a modified end grate zone where these fine particles fall through narrow gaps of predefined width between the grate elements, supported by a mechanical back and forth movement and special deflectors on the grate. The Grate for Riddlings is compatible with both new and existing grate installations.
Download: Brochure InovaRe
Combustion Control System AutaroTM
AutaroTM combustion management system that doesn’t only produce steam on a stable basis.
The main job of a combustion control system is to ensure even plant operation and the constant production of steam. Another key factor is flexibility. Fluctuations in waste compositions and calorific values at different plants require correspondingly flexible processes – and thus the right control system. This is also important if the waste does not burn as desired. In such a case it must be dried and moved, and oxygen must be fed in additionally.
Reference: Lausanne
More information: Brochure AutaroTM
Pamela Remote Monitoring
Pamela is an analysis tool developed specifically for WtE plants, designed to enhance their process and operation. It features a powerful web application with graphic analysis of the data collected. An automatic reporting function generates a daily report which is sent to the plant operator and Kanadevia Inova. Thanks to the user-friendly app and the Pamela shift book, the operator is constantly informed on the current operation of the plant.
References: Vantaa, Vaasa, Cleveland 3, 4 & 5, Lucerne, Ferrybridge, Horgen, Buckinghamshire, Poznan, Severnside, Jabalpur, Dublin, Edinburgh
Kompogas® Plug-Flow Digester
The Kompogas® plug-flow digester’s water- and gas-tight construction assures a high level of operational safety and 100% availability. An agitator mixes and degases the substrate at low drive power and prevents sedimentation. For this reason, Kompogas® digesters can also be used to treat organic waste with a high proportion of foreign matter. Multiple digester modules can be combined to create larger plants. The digesters are also ideal for retrofitting existing installations.
References: Winterthur, Werdhölzli, Högbytorp, Jönköping, Epirus, Foligno, Nanjing
KOM+Press
Kanadevia Inova’s KOM+Press dewatering press separates liquid and solid digestate with power and precision. Its service-friendly design results in lower operating costs and a longer lifetime. As well as being used in Hitachi Zosen AD installations, it is also a good upgrade or replacement for existing dewatering equipment.
References: Uzwil, Aarberg, Utzenstorf, Wauwil, San Luis Obispo, Högbytorp, Jönköping
Kanadevia Inova SpeedScreen
Kanadevia Inova SpeedScreen is a dewatering screen for the after-treatment of liquid digestate. It works by rotation to sieve sand and organic fibres out of the liquid digestate to optimally prepare them for processing downstream or storage. It does all this without the need for rinsing water, flocking agent or other additives. The robust design is geared to 24/7 operation and is extremely maintenance-friendly.
References: Jönköping, Högbytorp
Computerised Maintenance Management System – CMMS
Our computerised maintenance management system (CMMS) helps operators reliably plan and carry out plant maintenance. The program encompasses lists of consumables, service and lubrication schedules, lists of spares and wear parts, documentation, service rules and standards, as well as training, instructions and guides. It is set up according to the individual needs of the client and can be linked to diverse other programs, for example Kanadevia Inova Pamela.
Pamela Remote Monitoring
Pamela is an analysis tool developed by Kanadevia Inova to enhance the process and operation of WtE and biogas plants. It features a powerful web application with graphic analysis of the data collected. An automatic reporting function generates a daily report which is sent to the plant operator and Kanadevia Inova. Thanks to the user-friendly app and the Pamela shift book, the operator is constantly informed on the current operation of the plant.
References for AD: Zurich, Winterthur
Swapping Out Activated Carbon
We replace your biogas upgrading installation’s activated carbon quickly and cleanly. We can offer the service both for Kanadevia Inova BioMethan equipment and for most filter types at installations from other providers. We organise appropriate disposal at short notice.
Changing Amine
We power down your plant safely to service mode, remove the used amine and rinse the entire process stage through thoroughly. Then we fill up with fresh amine and rapidly put your plant back in feed-in mode. We organise appropriate disposal at short notice.
Swapping Out Heat Exchanger Plates
We power down your plant safely to service mode and remove used amine from the relevant process stage. Depending on the degree of wear, only individual plates or the entire heat exchanger will be replaced to keep the repair costs as low as possible for you.
Pressure Testing
We organise deployment of the inspection authority responsible, prepare the plant and provide the necessary testing equipment. Our trained service staff perform the pressure testing on site. We’ll be glad to keep track of recurrent testing dates and deadlines on your behalf and coordinate them with you.
Changing Bearings
If your compressors malfunction we’re there for you at short notice, for example to professionally replace damaged bearings, seals or diverse other components. That way your plant is ready to switch back to feed-in mode as quickly as possible.
Changing Drying Agent
We’ll be glad to prepare your plant, removing the relevant insulating material and piping. Our well-equipped cooperation partner will pump off the drying agent and dispose of it appropriately. The vehicle has special pumping equipment to refill the plant with new drying agent quickly and cleanly so that it can rapidly return to regular operation.
Checking Flame Intensity
To ensure the reliable deployment of the flares, we’ll be glad to check the individual components and subsystems. This also includes cleaning the UV sensor and setting the starter correctly.
Changing Bearings
If your compressors malfunction we’re there for you at short notice, for example to professionally replace damaged bearings, seals or diverse other components. That way your plant is ready to switch back to feed-in mode as quickly as possible.
Activated Carbon
We replace your biogas upgrading installation’s activated carbon quickly and cleanly. We can offer the service both for Kanadevia Inova BioMethan equipment and for most filter types at installations from other providers. We organise appropriate disposal at short notice.
Oil Service
We pay particular attention to the screw compressor, the centrepiece of your treatment plant. Our specially trained service staff will change the oil, and also have a modified service kit to also replace wear parts at the same time if necessary. This minimises downtime.
Cleaning Service
We coordinate with you so that your plant is turned off in advance, and bring special tools to clean the tube bundles. This way we can carefully clean the component and maintain good heat transmission for as long as possible.
Changing Filters
During the service you can have us take samples and do quality analyses. They will be evaluated by our experts as a basis for determining measures, for example changing filters.
Changing Modules
We’ll be glad to run a membrane performance test for you on our special test bench. This way inefficient membrane modules can be identied and replaced as necessary by our service staff. Doing this rather than changing the entire membrane modules considerably reduces maintenance costs.
Checking Flame Intensity
To ensure the reliable deployment of the flares, we’ll be glad to check the individual components and subsystems. This also includes cleaning the UV sensor and setting the starter correctly.
Kanadevia Inova Feed Hopper
The Kanadevia Inova Feed Hopper consists of individual water-cooled modules. The interior surfaces are made of wear-resistant materials to withstand heavy use. Depending on the position of the individual modules and the stresses to which they are subject, they are made of different materials and can be repaired or replaced independently of each other. The Kanadevia Inova feed hopper is incorporated in the existing steel structure, adapted in line with the specific circumstances This makes it the ideal retrofit for a range of WtE plants.
References: Zorbau, Zisterdorf, Umea
Download: Kanadevia Inova Feed Hopper Brochure
Inova Grate
The new Inova Grate is a reciprocating grate with physically separated grate zones and individual reciprocating grate elements. The grate is built to be inclined at a lower angle, allowing a lower and more compact design and reducing the space required. At the same time larger grate blocks enable the subsequent costs of operation to be reduced. The size of the grate and the appropriate cooling system (water or air) are determined on the basis of the combustion diagram and the specific requirements of the plant and the waste processed.
References for Inova Grate: Lucerne, Poznan, Ivry*, Rockingham*
*Under construction
Kanadevia Inova R-Series Grate
The R-Series incinerator grate developed in-house by Kanadevia Inova is a reciprocating grate inclined at an angle of 18° with individually movable grate elements. This feature enables operational flexibility and ensures that the waste is transported, mixed and combusted efficiently. The R-series grate is air-cooled as standard. The size of the grate is determined on the basis of the requirements specific to the plant and the waste it treats.
References: Cleveland 3, 4 & 5, Riverside, Newhaven, Jabalpur, Severnside, Dublin, Edinburgh, Moscow 1*
*Under construction
Grate Cooling
All our grates can be built with water or air cooling, with the choice depending on the combustion diagram and the specific requirements of the plant and the waste processed. Air cooling makes sense if the calorific value of the waste is low to average. Here the primary air is also used to cool the grate. For waste with a higher calorific value a water-cooled grate makes more sense. By decoupling grate cooling from the air supply, the air supply also enhances the combustion process, resulting in better quality bottom ash and less flue gas.
References for air cooling: East Rockingham*, Newhurst*, Rookery*, Moscow 1*, Istanbul*, Edinburgh, Dublin, H&W, Poznan, Severnside, Jabalpur, Buckinghamshire
References for water cooling: Ivry-sur-Seine*, Ferrybridge 1 + 2, Horgen, Lucerne, Vantaa, Vasaa, Oslo
Low Excess Air Process (LEAP)
Our staged combustion process consists of two injection stages for secondary air and recirculated flue gas. LEAP reduces the combustion air flow rate in your installation, enabling the use of smaller components for the boiler and flue gas treatment system. Even distribution of corrosive agents thanks to intense mixing also reduces the risk that the boiler will corrode, even at lower oxygen levels.
References with flue gas circulation: Lucerne, Dublin, Oslo, Lausanne
References without flue gas circulation: Vaasa, Horgen
Download: LEAP brochure
Boiler
We design and build custom boilers, both horizontal and vertical. Our compact design enables us to make the best possible use of the space available and optimise the flow of exhaust gases even if space is limited.
References for horizontal boiler passes: Moscow*, Istanbul*, Ferrybridge I+II, Edinburgh, Hereford & Worcestershire, Dublin
References for vertical boiler passes: Jabalpur, Cleveland 4&5, Poznan, Bamberg, Barcelona, Pithiviers, Stassfurt, Cleveland 3
*Under construction
Kanadevia Inova Primary Air Filter
Primary air is sucked out of the waste bunker to prevent emissions of dust and odors into the environment. The primary air filter cleans this air so that the primary air preheater becomes dirty less quickly. This avoids the need for cleaning services and allows the plant to run continuously for longer.
References: Thun
Monitoring the Boiler Rapper System
Kanadevia Inova’s boiler rapping monitoring system checks the functional integrity of the rapper during operation. If the function of a harp is found to be limited, the system automatically increases the rapping force and adjusts the rapping frequency while simultaneously alerting the operator. The online monitoring tool is suitable for both mechanical and pneumatic rappers.
Download: Online Boiler Rapper Brochure
DyNOR®: Kanadevia Inova’s Advanced SNCR Process
The DyNOR® system developed by Kanadevia Inova’s engineers is an improved selective non-catalytic reduction (SNCR process). It enables nitrogen oxide to be reduced to very low levels with minimal ammonia slip, something that was previously only possible with an SCR (selective catalytic reduction) process. The non-catalytic DyNOR® process closes the gap between the costly SCR process and the conventional SNCR process.
References: Vaasa, Vantaa, Severnside, Dublin, Poznan
Download: Brochure Dynor SNCR Process
Dry Sorption: XeroSorp Bicar/Lime
Dry sorption involves neutralising acid gases by with neutralising additives, but without water. In our XeroSorp process we use hydrated lime of sodium hydrogen carbonate (sodium bicarbonate). The system is outstanding in terms of low investment and operating costs, and requires little space in your installation.
References: Bellegarde*, Istanbul*, Edinburg, Lucerne, Horgen, Issy-les-Moulineaux
Semidry Sorption Process (Kanadevia Inova SemiDry)
The Kanadevia Inova SemiDry system involves a semidry sorption process employing the principle of the circulating fluidised bed. Hydrated lime and water are injected in to neutralise acid gases. The system is a highly effective means of reducing emissions and is very flexible in terms of a range of process factors. This all makes it very popular in the industry.
References: Dublin, Ferrybridge 1+2, Hereford and Bedfordshire, Poznan, Severnside, Buckinghamshire, Cleveland
Kanadevia Inova Pulse Jet Monitoring
Kanadevia Inova’s pulse jet monitoring system monitors and controls the cleaning of the filter chambers. It uses the measurement data gathered as the basis for coordinating the selective cleaning of filter bags and regulates cleaning sequences for individual filter bag lines. Thanks to high-performance sensors, the automated control system to instantly detects valve failures and damage to bags, and displays the position and type of defect for the operator.
Wet Scrubbing Kanadevia Inova WetScrubber
Wet scrubbing is the most effective method for removing acid gases from even heavily burdened flue gases, achieving the lowest emissions. The process is also excellent for removing fine particulate and aerosols. The Kanadevia Inova WetScrubber consists of multiple stages that can be combined on a variable basis to tailor the process individually to the client’s requirements.
References: Dublin, Oslo, Trondheim, Lausanne
Download: Brochure Oxi-Air – Wet Scrubbing
Kanadevia Inova RingJet
The ringjet stage is a very typical component of wet scrubbing. Placed in the scrubber, Kanadevia Inova RingJets produce a mist of water that separates fine particulates and aerosols from the exhaust air or flue gases. Laden with pollutants, the droplets are then removed. The Kanadevia Inova RingJet is easy to fit, robust and to a large extent maintenance-free. It is space-saving, and can also be retrofitted to existing scrubbing towers.
References: Buchs, Oslo, Trondheim, Limmattal, Lausanne
Download: Brochure Kanadevia Inova RingJet
Kanadevia Inova CondensingScrubber
In addition to the benefits of the Kanadevia Inova WetScrubber, the Kanadevia Inova CondensingScrubber allows heat to be recovered by condensing the water vapour contained in the flue gas. This way a plant can achieve overall energy efficiency of more than 100%.
References: Oslo
DeNOx Systems
We use different SCR (selective catalytic reduction) and SNCR (selective non-catalytic reduction) systems to remove the nitrogen oxides produced in the combustion process.
Kanadevia Inova DryMining
Kanadevia Inova DryMining is a fully automatic treatment process for recovering ferrous and nonferrous metals from bottom ash and the boiler ash. The tower installation can be used with wet or dry fine bottom ash discharge. The first step is to separate out the ferrous metals, before the nonferrous metals are sieved out and sorted by density. The process is controlled either from the control tower or with the help of a local switchboard.
References: Horgen, Emmenspitz
Download: Brochure InovaRe
Grate for Riddlings
Around 70% of valuable nonferrous metals are to be found in the <10 mm fine fraction of the bottom ash. Our Grate for Riddlings is geared to recovering this fine fraction. It contains a modified end grate zone where these fine particles fall through narrow gaps of predefined width between the grate elements, supported by a mechanical back and forth movement and special deflectors on the grate. The Grate for Riddlings is compatible with both new and existing grate installations.
Download: Brochure InovaRe
Combustion Control System AutaroTM
AutaroTM combustion management system that doesn’t only produce steam on a stable basis.
The main job of a combustion control system is to ensure even plant operation and the constant production of steam. Another key factor is flexibility. Fluctuations in waste compositions and calorific values at different plants require correspondingly flexible processes – and thus the right control system. This is also important if the waste does not burn as desired. In such a case it must be dried and moved, and oxygen must be fed in additionally.
Reference: Lausanne
More information: Brochure AutaroTM
Pamela Remote Monitoring
Pamela is an analysis tool developed specifically for WtE plants, designed to enhance their process and operation. It features a powerful web application with graphic analysis of the data collected. An automatic reporting function generates a daily report which is sent to the plant operator and Kanadevia Inova. Thanks to the user-friendly app and the Pamela shift book, the operator is constantly informed on the current operation of the plant.
References: Vantaa, Vaasa, Cleveland 3, 4 & 5, Lucerne, Ferrybridge, Horgen, Buckinghamshire, Poznan, Severnside, Jabalpur, Dublin, Edinburgh
Kompogas® Plug-Flow Digester
The Kompogas® plug-flow digester’s water- and gas-tight construction assures a high level of operational safety and 100% availability. An agitator mixes and degases the substrate at low drive power and prevents sedimentation. For this reason, Kompogas® digesters can also be used to treat organic waste with a high proportion of foreign matter. Multiple digester modules can be combined to create larger plants. The digesters are also ideal for retrofitting existing installations.
References: Winterthur, Werdhölzli, Högbytorp, Jönköping, Epirus, Foligno, Nanjing
KOM+Press
Kanadevia Inova’s KOM+Press dewatering press separates liquid and solid digestate with power and precision. Its service-friendly design results in lower operating costs and a longer lifetime. As well as being used in Hitachi Zosen AD installations, it is also a good upgrade or replacement for existing dewatering equipment.
References: Uzwil, Aarberg, Utzenstorf, Wauwil, San Luis Obispo, Högbytorp, Jönköping
Kanadevia Inova SpeedScreen
Kanadevia Inova SpeedScreen is a dewatering screen for the after-treatment of liquid digestate. It works by rotation to sieve sand and organic fibres out of the liquid digestate to optimally prepare them for processing downstream or storage. It does all this without the need for rinsing water, flocking agent or other additives. The robust design is geared to 24/7 operation and is extremely maintenance-friendly.
References: Jönköping, Högbytorp
Computerised Maintenance Management System – CMMS
Our computerised maintenance management system (CMMS) helps operators reliably plan and carry out plant maintenance. The program encompasses lists of consumables, service and lubrication schedules, lists of spares and wear parts, documentation, service rules and standards, as well as training, instructions and guides. It is set up according to the individual needs of the client and can be linked to diverse other programs, for example Kanadevia Inova Pamela.
Pamela Remote Monitoring
Pamela is an analysis tool developed by Kanadevia Inova to enhance the process and operation of WtE and biogas plants. It features a powerful web application with graphic analysis of the data collected. An automatic reporting function generates a daily report which is sent to the plant operator and Kanadevia Inova. Thanks to the user-friendly app and the Pamela shift book, the operator is constantly informed on the current operation of the plant.
References for AD: Zurich, Winterthur
Swapping Out Activated Carbon
We replace your biogas upgrading installation’s activated carbon quickly and cleanly. We can offer the service both for Kanadevia Inova BioMethan equipment and for most filter types at installations from other providers. We organise appropriate disposal at short notice.
Changing Amine
We power down your plant safely to service mode, remove the used amine and rinse the entire process stage through thoroughly. Then we fill up with fresh amine and rapidly put your plant back in feed-in mode. We organise appropriate disposal at short notice.
Swapping Out Heat Exchanger Plates
We power down your plant safely to service mode and remove used amine from the relevant process stage. Depending on the degree of wear, only individual plates or the entire heat exchanger will be replaced to keep the repair costs as low as possible for you.
Pressure Testing
We organise deployment of the inspection authority responsible, prepare the plant and provide the necessary testing equipment. Our trained service staff perform the pressure testing on site. We’ll be glad to keep track of recurrent testing dates and deadlines on your behalf and coordinate them with you.
Changing Bearings
If your compressors malfunction we’re there for you at short notice, for example to professionally replace damaged bearings, seals or diverse other components. That way your plant is ready to switch back to feed-in mode as quickly as possible.
Changing Drying Agent
We’ll be glad to prepare your plant, removing the relevant insulating material and piping. Our well-equipped cooperation partner will pump off the drying agent and dispose of it appropriately. The vehicle has special pumping equipment to refill the plant with new drying agent quickly and cleanly so that it can rapidly return to regular operation.
Checking Flame Intensity
To ensure the reliable deployment of the flares, we’ll be glad to check the individual components and subsystems. This also includes cleaning the UV sensor and setting the starter correctly.
Changing Bearings
If your compressors malfunction we’re there for you at short notice, for example to professionally replace damaged bearings, seals or diverse other components. That way your plant is ready to switch back to feed-in mode as quickly as possible.
Activated Carbon
We replace your biogas upgrading installation’s activated carbon quickly and cleanly. We can offer the service both for Kanadevia Inova BioMethan equipment and for most filter types at installations from other providers. We organise appropriate disposal at short notice.
Oil Service
We pay particular attention to the screw compressor, the centrepiece of your treatment plant. Our specially trained service staff will change the oil, and also have a modified service kit to also replace wear parts at the same time if necessary. This minimises downtime.
Cleaning Service
We coordinate with you so that your plant is turned off in advance, and bring special tools to clean the tube bundles. This way we can carefully clean the component and maintain good heat transmission for as long as possible.
Changing Filters
During the service you can have us take samples and do quality analyses. They will be evaluated by our experts as a basis for determining measures, for example changing filters.
Changing Modules
We’ll be glad to run a membrane performance test for you on our special test bench. This way inefficient membrane modules can be identied and replaced as necessary by our service staff. Doing this rather than changing the entire membrane modules considerably reduces maintenance costs.
Checking Flame Intensity
To ensure the reliable deployment of the flares, we’ll be glad to check the individual components and subsystems. This also includes cleaning the UV sensor and setting the starter correctly.