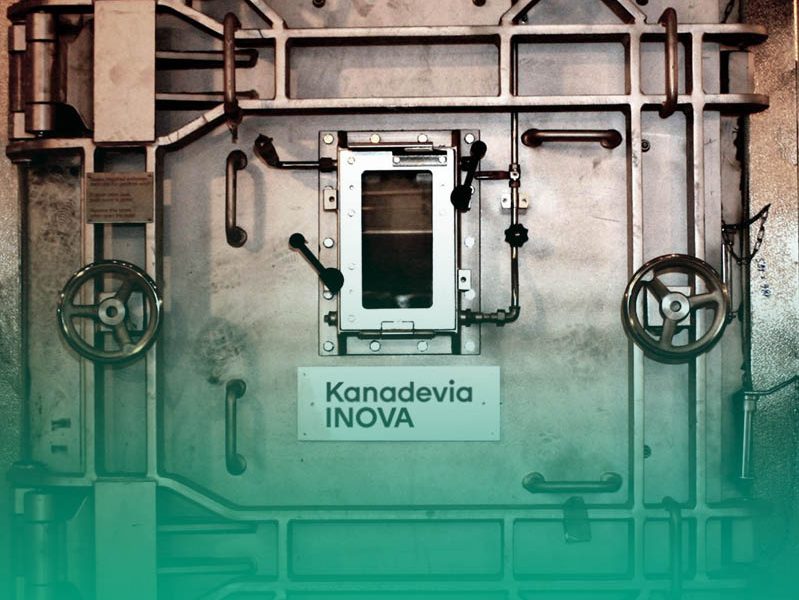
Incinerating waste produces exhaust gases laden with diverse pollutants. Different processes are used to remove these pollutants before the purified flue gas leaves the plant safely through the stack.
For decades Kanadevia Inova has been doing research into flue gas treatment and developing new and effective treatment systems. We harness internal synergies to optimally match and combine our combustion and flue gas treatment equipment. The numerous processes that have emerged can be used individually or together to create high-performance integrated systems.
The appropriate flue gas treatment approach is chosen in close consultation with the client. The selection criteria include regulatory air pollution limits, the client’s expectations regarding the energy efficiency of the plant, restrictions on waste water discharge, and the space available on site – to name only a few.
Various pollutants are introduced into the combustion process by the waste, including oxidised combustion products such as SO2and NOxproducts, as well as substances such as hydrogen chloride and hydrogen fluoride, heavy metals, dioxins and furans. We use specific types of treatment to separate these pollutants out during the WtE process and then dispose of them appropriately. Our comprehensive range of processes enables us to cover a broad spectrum of requirements.
Thanks to many years of experience, Kanadevia Inova can now offer a wide range of high-performance processes for reducing emissions. On the basis of the individual requirements and circumstances of each plant, we develop tailored integrated flue gas treatment approaches. When putting together the right overall approach we take account of the following factors:
Each flue gas treatment module serves a specific purpose. Flue gas cleaning achieves the highest performance when the various components are combined – on the basis of the individual requirements of the plant. In this way, even the lowest BREF emission values can be achieved without difficulty.