Waste is our Energy / Kanadevia Inova
Waste is our Energy
Kanadevia Inova
We Build Turnkey Waste to Energy Plants with Our Own Technologies
The Swiss green-tech company Kanadevia Inova AG (HZI) is a global leader in technology for energy and material recovery from municipal solid waste (MSW), refuse derived fuels (RDF) and organic waste.
We have been building and maintaining Waste to Energy (WtE) plants since 1933 and have been part of Hitachi Zosen Corporation since 2010. We support our customers in project development and draw on our experience as a general contractor to undertake the engineering, procurement and construction (EPC) of complete turnkey plants for the thermal and biological recycling of waste, biogas production and power to gas, as well as system solutions.
With our comprehensive after-sales services we provide expert and reliable support for existing plants. Our solutions are based on our own efficient, environmentally-friendly technologies. They are thoroughly tested, can be flexibly adapted to user requirements and cover the entire life cycle of a plant. Kanadevia Inova’s customer base ranges from experienced waste management companies and municipalities to farmers and emerging partners in new markets worldwide. Our innovative and reliable solutions are part of more than 1,600 reference projects all over the globe.
Kanadevia Inova: Portrait
We deliver. Check our 1,600 references worldwide.
“In the past, Kanadevia Inova and Hitachi Zosen Corporation ran their businesses in separate geographical areas. But going forward, by harnessing the resources and specialities of both parties effectively, we will be able to open up new markets, optimise procurement and share engineers and other personnel, which will boost our competitiveness in the global market.”
Michi Kuwahara, President and Chief Operating Officer, Hitachi Zosen Corporation
Pioneer in Thermal Waste Treatment
Kanadevia Inova’s roots go back to the foundation of L. von Roll Aktiengesellschaft in 1933, set up to focus on thermal waste treatment. Six years later, it built its first plant in the Dutch city of Dordrecht.
Emphasis on Technology
From the very beginning, the Swiss company developed proprietary and improved technologies including the reciprocating grate, advanced methods for flue gas cleaning and processes for the recovery of materials from residues.
Global Expansion
In 1960, von Roll entered into a long-term licence agreement with Hitachi Zosen Corporation and opened its first offices in Germany and Japan. Subsidiaries were founded in France and Sweden in 1966, and in 1975 the
company established a presence in the US. Since 2010, the Kanadevia Inova Group has been part of Hitachi Zosen Corporation. Additional entities have been opened in the UK, Slovakia, Australia and the UAE.
Reliability as a Commitment
In close cooperation with the customer, Kanadevia Inova is always on the lookout for the best and most environmentally compatible solutions. Our WtE and Renewable Gas technologies are part of more than 1,600 reference plants worldwide.
First-Class Waste Management Technologies and Services
In addition to Kanadevia Inova’s grate combustion and flue gas treatment technologies, Kanadevia Inova’s portfolio is rounded off by technologies for anaerobic digestion of biowaste, gas upgrading and conversion of electrical
energy into gas (Power to Gas). Passionate expert service teams support customers with the maintenance, retrofitting and analysis of existing equipment. Whatever the product or service, the customer also benefits
from Kanadevia Inova’s extensive research and development and its high-quality manufacturing capabilities.
Waste: A Global Challenge We’re Taking On
More Waste
The global volume of waste is growing faster than the world’s population. Despite increased waste prevention strategies, annual waste generation is expected to reach 3.4 billion tonnes by 2050.
Less Landfill Capacity
A lack of landfill capacity, high greenhouse gas emissions, the negative impact on the environment and urban hygiene, increasing costs and tighter regulations require alternative solutions.
Demand for Energy and Resources
Demand for alternative and renewable resources is increasing and recovering energy as well as raw materials from waste is becoming more important.
Away from Landfill…
Landfills account for five per cent of total human-made greenhouse gas emissions. The negative impact on human habitat and our environment would be substantially reduced by replacing landfills.
…to a Circular Economy
Separate collection of direct recyclables and organic waste allows material and energy recovery. Anaerobic treatment of organic waste produces biogas and natural fertiliser, while thermal treatment is used to recover energy and materials from waste that cannot be recycled directly.
“Converting non-recyclable waste materials into electricity and heat creates a renewable energy resource, cuts carbon emissions by offsetting the need for energy from fossil sources and reduces methane generation from landfills.”
The United States Environmental Protection Agency
Collection, Separation…
The first steps in a sustainable waste management system are the complete but reduced collection of waste as well as the separation of waste fractions that have a market value for recycling.
…and Waste to Energy…
Recovery of materials and energy from waste using thermal and biological waste treatment is an integral part of any modern waste management system focused on maximising utilisation of all resources contained in the
waste and minimising the adverse impact on society and the environment.
…Serve to Protect Human Habitat…
Waste to Energy not only decreases the volume of waste; it conserves natural resources such as land and water. It also protects the air and climate because WtE plants reduce the greenhouse gases coming from landfill.
…and Ensure Sustainable Recycling
A modern waste management system not only focuses on protecting health and the environment, but also makes maximum use of waste to reduce the exploitation of our limited natural resources. Kanadevia Inova has
first-class in-house technologies for sustainable waste management aimed at bringing the world closer to a circular economy.
We Deliver Turnkey Plants
Engineering, Procurement and Construction
Kanadevia Inova acts as a global EPC contractor for thermal and biological WtE plants as well as plants for producing methane from raw gas, capturing carbon dioxide (CO₂) and converting energy into gas. We are committed to delivering to our clients on schedule, within budget and with a keen focus on safety and quality. We execute turnkey projects in international markets based on our wealth of experience in managing a wide range of projects, from equipment supply to complete plant delivery.
Turnkey Plants
Kanadevia Inova assumes overall responsibility for the construction of complex WtE plants. The concept and plant design for integrated solutions are based on our highly reliable technologies. Our success comes from decades of experience in planning and building turnkey plants around the world. Our turnkey capabilities cover all relevant EPC tasks, ranging from engineering to plant commissioning. Leveraging its innovative spirit and project management competence, Kanadevia Inova guarantees highly efficient, forward-looking solutions that fully meet customer needs. Our project teams assure smooth project progress, timely coordination of suppliers and sub-contractors and compliance with the relevant technical, commercial and regulatory requirements.
Health and Safety
Our health and safety strategy focuses on providing a safe and healthy working environment for all our employees and partners, with the aim of zero incidents.
Quality Management
The quality of our products and services is key to the satisfaction of our customers. As quality is so essential to the success of our company, Kanadevia Inova introduced a comprehensive quality management system in accordance with the ISO 9001 standard back in 1992, and the system has been certified ever since.
All from a Single Provider
With us, your WtE projects are in good hands. We are capable of performing virtually any task relating to thermal and biological WtE. Our services include plant design and construction, project development, plant operation and maintenance, and equipment servicing.
“Kanadevia Inova is one of the major players on the market and has proven in-house technologies and relevant capabilities for the supply of turnkey WtE plants. We operate WtE plants
that Kanadevia Inova has delivered as a professional and reliable EPC contractor.”
Jean Erkès, Senior Vice President Recycling and Recovery Projects, Suez
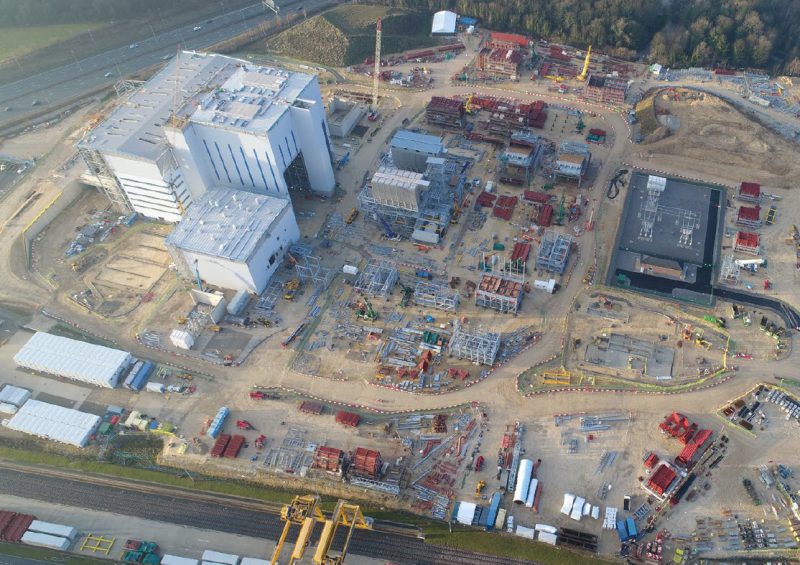
WtE plant under construction in Ferrybridge, UK
We Recover Energy and Materials from MSW and RDF
Kanadevia Inova’s Sustainable Thermal WtE Technology
Long-term, proven WtE solution with grate combustion, energy utilisation, flue gas treatment and materials recovery
Thermal WtE: Grate Combustion
“Reliable, well proven technology and innovative solutions from Kanadevia Inova ensure highly efficient energy recovery combined with optimal materials recycling and minimise the adverse impact on
the environment. We see this every day in our plant delivered by Kanadevia Inova.”
Olli Alonhiemi, Managing Director, Westenergy Oy Ab
Thermal Treatment of Waste: an Efficient, Environmentally Sound Solution for Modern Cities
Mixed municipal solid waste or RDF from sorting plants is delivered to the site and stored in a bunker. A crane thoroughly mixes the waste and feeds it into the feed hopper. From there it is pushed onto the grate by a ram feeder. A fully integrated control system ensures stable and efficient staged combustion and optimised burn-off loss on the grate. Once combustion is complete, the bottom ash falls into the wet or dry bottom ash extractor, from where it can be taken to a treatment facility for metal recovery and reuse of the inert material in road construction. The flue gases from combustion are cleaned to the strictest standards in the downstream flue gas treatment system and are continuously monitored before being released into the atmosphere via the stack. The energy in the flue gases is used to produce superheated steam, which is expanded in a turbine generator
to produce electricity. Alternatively, the heat can be used for process steam supply or also combined with the heat from flue gas condensation for district heating purposes.
Kanadevia Inova’s thermal WtE plants are designed custom-fit for a wide variety of heating values, throughputs and energy recovery methods. You can rely on the experience Kanadevia Inova has gained in over 600 reference plants over more than 90 years, using our own technologies to deliver the highest energy efficiency and environmental compatibility and lowest residue production.
Combustion Systems
Reliable Technology: Continuously Improved and Optimised
Grate combustion is the best-proven thermal waste treatment technology. Thanks to continuous optimisation, today’s grate combustion is the most advanced technology with regard to environmental friendliness, operating reliability, flexibility and cost-effectiveness. Kanadevia Inova’s state-of-the-art grate combustion technology, developed in-house, is specially designed for the thermal treatment of municipal solid waste and RDF.
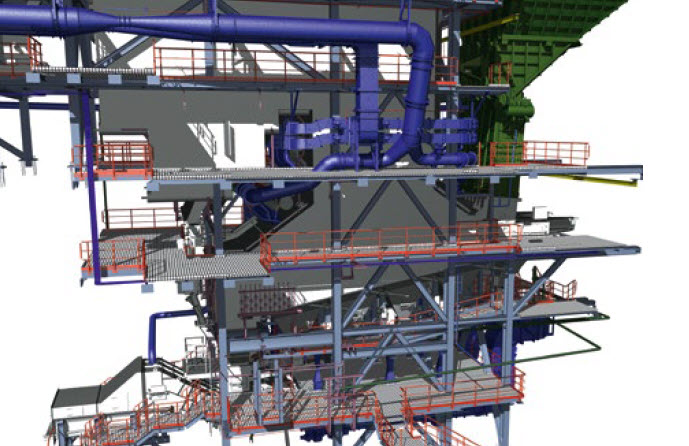
Kanadevia Inova grate combustion
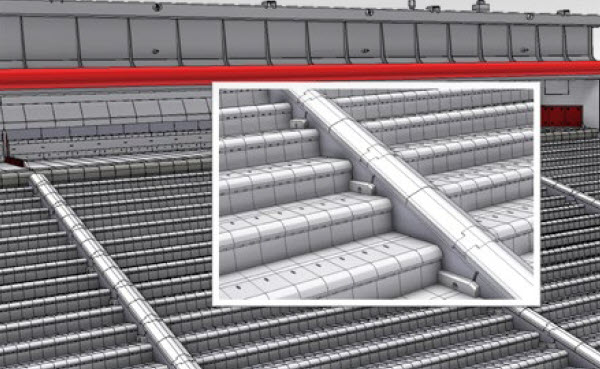
Inova Grate
Well-proven Combustion Technology
The Kanadevia Inova combustion system consists of coordinated units such as feed, grate, primary and secondary air systems, ash discharge and an efficient and reliable boiler. A fully integrated process control system ensures stable
combustion and optimised burnout. The gases from the waste bunker serve as primary air. Secondary air is injected above the grate. This ensures complete combustion and minimises CO, NOx and VOC emissions.
Optional flue gas recirculation and/or lower excess air also improve the energy efficiency of the system.
Inova Grate
Our patented Inova Grate consists of individual grate modules with alternating rows of fixed and movable grate blocks. The hydraulically-driven movable grate blocks stoke the waste and convey it through the combustion
chamber for optimum burnout. The layout and design of the grate are adapted to the individual requirements and properties of the waste. The same applies to the cooling system: the air-cooled grate, with its stable design, is the most advantageous solution in terms of investment and maintenance costs, depending on the waste characteristics.
With high thermal loads, water-cooled grate blocks provide a longer service life with a decisive advantage: the air flow can be precisely controlled in each grate zone.
Flue Gas Treatment
Clean Air thanks to Kanadevia Inova Technologies
Emission limits for WtE plants are more stringent than for any other thermal power plant. This requires the best available technologies (BATs). Kanadevia Inova offers a range of effective and proven flue gas treatment processes that can be used to extract and neutralise the pollutants.
Dry and Wet Systems
Individual flue gas cleaning modules are chosen and designed according to local requirements and emission limits. In the dry sorption process, we remove acidic pollutants with our patented XeroSorp® process using
hydrated lime or sodium bicarbonate. This achieves high efficiencies with low amounts of residual material. As its name suggests, the Kanadevia Inova SemiDry system uses a semi-dry process based on the principle of the circulating
fluidised bed, and removes acid pollutants with lime hydroxide and water. It guarantees low emissions and is extremely resistant to changes in pollutant concentration in the exhaust gas.
Wet scrubbing is the most effective method for removing acid pollutants – even from heavily loaded flue gases. Here the pollutants are separated by intensive contact between the flue gases and water or by adjusting the pH
value. A condensation scrubber enables additional heat extraction.
NOx Elimination
Kanadevia Inova offers two proven processes for the elimination of nitrogen oxides: selective catalytic reduction (SCR) and selective non-catalytic reduction (SNCR). Thanks to catalysis, the SCR process achieves the highest separation
rate for NOx, dioxins and furans, with the lowest reagent consumption. In the SNCR process, nitrogen oxides are converted into nitrogen and water vapour with the addition of ammonia. This system is used successfully
in many places thanks to the low infrastructure and process costs involved.
The DyNOR® process developed by Kanadevia Inova is a link between conventional SNCR and the complex SCR process. Thanks to precise temperature measurements, ammonia injection is carried out in a very targeted manner, which
minimises ammonia slip and significantly reduces process costs.
Energy Recovery
Economical, Reliable, and Efficient
Recovering the energy content of waste is the key function of WtE plants. The recovered energy is used in the way that best meets the needs of the customer. Cogeneration, the simultaneous production of electric power and heat, offers high efficiency and maximum energy yield.
Electric Power: Proven Base-Load Power
WtE plants are already proven suppliers of base-load energy in many places, which increases the share of renewable energies in the energy mix. By controlling the combustion process in a targeted manner, energy can
also be fed into the grid as needed during energy peaks. For electricity production, superheated steam from the boiler drives a steam turbine that is connected to a generator. The electricity produced by the generator is fed
into the public grid.
Thermal Power: District Heating or Industrial Use
Using the heat increases the overall efficiency of the system. The heat is either made available directly as process steam for industrial use or fed into the public district heating network as hot water.
Combined Heat and Power and Cold and Power
Although a higher heat output reduces electricity generation, the combination of electricity production and heat output increases the overall energy efficiency of the plant. In addition to classic combined heat and power in
the form of district heating or process steam, the concept of cold and power creates a cooling option in countries with high temperatures. For this purpose, steam drives an adsorption cooler that converts heat into cold water which is then transported to consumers via a district cooling network.
Materials Recovery
Reusing Most Materials
Thermal waste treatment plants produce bottom ash and flue gas treatment residues which can be recovered and profitably reused. With Kanadevia Inova’s intelligent secondary treatment process, large parts of these materials are brought back into the circular economy.
Efficiently Recovering Metals from Waste
Recovering recyclable materials from residues is an increasingly relevant part of urban mining for operators of WtE plants. This urban mining has
four key benefits:
– Generates additional revenues from the sale of recovered materials such as iron, copper, aluminium, gold, minerals and salts
– Reduces disposal costs thanks to lower quantities of residue
– Makes a relevant contribution to environmental protection and sustainability. By providing recyclable materials, the operator contributes to the conservation of resources, reductions in CO₂ emissions and the circular economy principle
– Meets the legal requirements governing the recovery of recyclables from waste, which are already mandatory in some countries and regions.
Fly Ash Washing: Stabilisation and Product Recovery
If fly ash is collected separately from bottom ash and flue gas cleaning residues, two different methods may be applied to remove or immobilise it. Acid washing fly ash using acidic scrubber blowdown removes heavy metals
in a recyclable form and produces a fly ash which can be disposed of with the bottom ash. Neutral washing is followed by solidification to condition the fly ash into a leach-resistant matrix which can then be used for construction purposes.
Effluent Treatment: Capturing and Recycling Contaminants
The effluent treatment process neutralises blowdown from wet flue gas scrubbers or fly ash washing and removes contaminants such as heavy metals, ammonia and persistent organic pollutants. Depending on the
plant configuration, some contaminants such as mercury or zinc can be recovered for recycling. The only remaining components in the cleaned effluent are naturally occurring salts such as sodium and calcium chlorides and sulphates.
We Recover Energy and Materials from Organic Waste and Biogenic Raw Gas
Integrated solutions for recovering renewable energy and various recyclable materials, wet and dry digestion, upgrading biogenic raw gases, carbon capture and converting electricity to storable gas for a secure and future-oriented energy landscape
Biological WtE: Kompogas® Dry Anaerobic Digestion
Kompogas® is the Market and Technology Leader in Dry Digestion Processes
The patented Kompogas® process is based on the continuous dry fermentation of organic waste using a horizontal plug-flow digester. In this process the temperature in the digester is maintained at 55° Celsius. The average moisture of the digester’s contents is around 75% and the retention time is approximately 14 days. The Kompogas® process ensures that the organic waste is fully converted to biogas and that the digestate is completely sanitised. The continuous, horizontal plug-flow digester allows a high biogas yield and maximises operating reliability thanks to simple and efficient control systems. A low-speed agitator ensures optimum biogas conversion. The special design of the agitator paddles prevents sedimentation of heavy and undesired matter in the substrate. Fermentation involves various upstream and downstream processes. In the feed unit, the organic waste is shredded and metals and other non-digestibles are removed. A discharge pump withdraws the digestate. Around one-third is pumped back for inoculation. The rest is either dewatered to produce compost and liquid fertiliser or mixed with green waste using the liquid fertiliser-free partial flow process.
“The Kompogas® technology allows us to transform organic waste energetically into biogas and energy, and to recycle the waste in the form of solid and liquid fertiliser. With this technology, we are contributing to sustainable waste management in the Botarell area.”
Hugo Urdaneta, Plant Manager, Botarell Kompogas® plant in Spain
Core Component of the Patented Kompogas® Process
Our digesters are available in two series as concrete or steel digesters. Both series are equipped with the same robust agitator components and can be deployed for all input materials, biowaste, green waste and organic elements from general waste collection. Two, three or more digester modules can be combined to form larger plants.
Precise Dewatering Systems
Thorough dewatering of the digestate ensures the recovery of valuable solids and the efficient preparation of the liquid digestate for further processing or storage downstream. This has prompted Kanadevia Inova to further develop the dewatering process. Our in-house dewatering press, the Kanadevia Inova KOM+PRESS, and our improved dewatering screen, the Kanadevia Inova SpeedScreen, thoroughly dewater the digestate and, thanks to their user-oriented design, are extremely service-friendly and low-cost to operate.
Energy from Biogenic Raw Gases: Gas Upgrading and Carbon Capture
Energy Concepts for the Future
Kanadevia Inova BioMethan supplies gas upgrading plants in which biogenic raw gases are processed into biomethane and high-purity carbon dioxide. These gases from renewable sources replace those of fossil origin and contribute
to decarbonisation. Two different processes are used to separate CO₂ from the methane contained in raw biogases: amine scrubbing and the pressurecontrolled membrane process.
Amine Scrubbing
In amine scrubbing, the pre-cleaned raw gas flows through a scrubbing column with an amine scrubbing unit. This absorbs the CO₂ contained in the raw gas. Meanwhile, the resulting high-purity biomethane is withdrawn at the top of the column. The process is suitable for locations with an existing heat source and high product gas requirements. The pressure for the transfer from gas upgrading to the feed-in station can be adjusted as required.
“Thanks to their many possibilities, these technologies can be used to expand existing facilities like ours in Nesselnbach. For example, we’ve been able to retrofit our biogas/biomethane plant with CO₂ liquefaction technology and gear it to future-proof operation that’s economically viable in the long term.”
Philippe Lehmann, CEO of biogas upgrading and CO₂ utilisation specialist, CO2 Energie AG
Membrane Technology
In membrane-based gas permeation, the raw gas is introduced into the membrane modules after further pre-treatment. These modules consist of several thousand polymer hollow fibre membranes bundled in a stainless-steel housing. The separation of CO₂ and methane takes place by selective permeation: owing to the different transport speeds and solubilities in the polymer, CO₂ permeates through the surface of the membranes more quickly than methane. The methane is retained in the membranes and removed from the modules as product gas at the end of the process. This physical process is suitable for locations with favourable, stable and calculable electricity
costs, with small and fluctuating raw or feed gas quantities and a high required transfer pressure.
Waste to X Technologies in Use for the Future
Flue Gas Scrubbing through Carbon Capture
Carbon capture technologies can also be used to purify waste gases from industry and commerce. The customer can choose between two separation processes: amine scrubbing or membrane technology. The CO₂ can then be marketed as product gas for customers in the pharma and food industries, for industrial processes, but also for plant cultivation. The advantage is that in liquefied form, CO₂ generation and use can be decoupled from each other. Companies benefit not only from the additional yield, but also from an improved carbon footprint.
Wet AD: Partner to Farmers, Municipal Utilities and Energy Providers
Biogas is a major source of renewable energy. Unlike wind and solar power, biogas can be produced on a predictable basis from replenishable, locally available waste and residues. This enables the reliable production of electricity, heat, gas or vehicle fuels – renewable resources that are crucial to the global energy transition.
Sustainable Transport
Biomethane is fed into the natural gas grid and is also used as compressed biomethane at filling stations for natural-gas-powered vehicles. However, this renewable energy resource is particularly important in liquefied form for heavy goods and long-distance freight transport. In contrast to compressed natural gas/bio-natural gas, LNG/LBG enables long ranges with small tank volumes. Electric vehicles have not been an alternative for this transport segment to date, so LBG offers unprecedented advantages: increasing the share of renewable energy in the fuel mix, reducing greenhouse gas and NOx emissions as well as air pollutant and noise pollution. Not only that, but proven vehicle and refuelling station technologies are already available.
Power-to-Gas Technology of the Future
Our Power to Gas (PtG) technology puts us at the fulcrum of the modern energy industry, enabling us to make electricity from volatile renewable energy resources storable and transportable at the same time.
The technology is used to produce synthetic gases such as hydrogen and methane from various types of raw gases. These synthetic gases are fed into the existing infrastructure and can be used at any time as fuel and heat or converted back into electricity. We use electrolysis and methanation technologies to generate hydrogen from electricity or produce other substitute natural or synthetic gases; CO₂ from raw or feed gases is converted instead of being released.
“Our Renewable Gasfield project, which combines green power generation, a biogas plant, electrolysis and methanation technologies, demonstrates the new possibilities in terms of carbon-neutral, integrated energy in the future.”
Dipl.-Ing. Klaus Neumann, Product Development Coordination, Energie Steiermark
BiON® Process: Biological Methanation Using Microorganisms
In the BiON® process, hydrogen and carbon dioxide are converted into pure methane, which can be injected into the natural gas grid in unlimited quantities. BiON® is therefore an all-round process serving as
an upgrade technology for process gases containing CO₂, as a power to gas application for storing green electricity and as production process for synthetic methane. The key to this crucial step in the energy
transition is special microorganisms. Thanks to these tough natural helpers, evolved to perfection over millions of years, this process offers huge potential and a raft of benefits.
Catalytic Methanation: Large-Scale Hydrogen and Carbon Dioxide Conversion
Kanadevia Inova’s catalytic methanation solution is designed to convert hydrogen, carbon dioxide and carbon monoxide into synthetic methane and water. Methane is an advanced and CO₂-neutral gaseous energy
carrier that can be readily stored and transported in existing natural gas infrastructures. Used directly in technology-proven end-devices, synthetic methane plays an essential role in decarbonising a wide range of applications in transport, energy and industry.
We Take Care of Your Plant
Comprehensive Services for the Entire Plant Life Cycle
Operation and Maintenance
For owners of WtE plants, the focus is on achieving maximum efficiency coupled with the highest economic benefit. Kanadevia Inova’s customers maximise the benefit from their investment. We work with our customers to develop an efficient strategy that will ensure their WtE plant performs optimally in terms of availability, waste throughput and energy recovery. Remote support is possible thanks to our special tool Pamela.
The plant can be monitored from our offices, giving us the full picture of all operational data. This allows us to make efficient decisions on interventions and optimising the operating conditions. Kanadevia Inova’s interactive training tool ITS simulates plant operations as well as covering health and safety aspects.
Retrofit
Tighter legislation and more stringent environmental and economic requirements are constantly presenting new challenges for plant owners. We provide holistic solutions and the latest technologies to help tap the full potential for efficiency and performance gains at any plant. This includes modernisation for extended service life, emission reductions for maximum ecological compatibility, and increased efficiency and higher steam output through constant supervision of heat exchangers. We focus on leveraging our resources to maximise your plant’s performance.
“With the retrofit of the grate, boiler, bottom ash extractor and flue gas treatment executed by Kanadevia Inova, we will be able to operate our plant for another fifteen years with greater energy efficiency
and a higher recycling rate.”
Romano Wild, CEO of the WtE plant in Horgen, Switzerland
Manufacturing
Kanadevia Inova Service specialises in manufacturing boiler parts and piping, and we pride ourselves on maintaining long-standing partnerships with our customers. Since 1997, we have been providing products and services around thermal waste treatment to our customers in Switzerland and abroad. The spectrum includes manufacturing for steam generators, fabrication of membrane walls and tube bundles, cladding for boiler and combustion systems, and constructing standard or customised components.
Spare Parts Management
Spare parts management is complex and cost-intensive and requires storage space. That is why it makes sense to entrust us with procuring and delivering wear components. We are quick, reliable and expert in the
field. Original spare parts are provided directly from stock. For our clients, this translates into savings in terms of expenditure and time.
Laboratory Services
Kanadevia Inova’s laboratory is equipped to meet the demands of WtE plant operators. Our range of services is as broad as the variety of questions arising in connection with thermal and biological waste treatment. We check compliance with emission limits and performance guarantees, measure the relevant process parameters and carry out root cause analysis in the event of operational problems. We bring together all the relevant WtE testing and analytical methods under one roof, including sampling, measurements and analysis on site, enabling very quick turnaround times.
Kanadevia Inova: Our Commitment
“What fascinates me about working at Kanadevia Inova is successfully tackling complex projects in interdisciplinary teams.”
Matthias Baur, Senior Sales Manager, Kanadevia Inova
“On the KEBAG Enova construction site we’ve experienced first-hand Kanadevia Inova’s proactive and rigorous approach to safety. It’s very effective, forward-looking and exemplary.”
Markus Juchli, Director of the Waste to Energy plant in Zuchwil-Emmenspitz, Switzerland
Kanadevia Inova as an Employer
Our employees come first: They are the key to our outstanding solutions. We offer our highly trained and qualified people a rewarding environment where motivation, team spirit, creative involvement and a philosophy
of leadership are all actively fostered and encouraged. We value our people and draw our strength from their drive, their passion for engineering, consulting and project management, and their in-depth expertise and experience.
Kanadevia Inova as a Partner
We strive to be a trusted partner to our clients and stakeholders all over the world. With over 90 years of experience, our aim is not only to build thermal and biological WtE plants worldwide, but also to be a fair
partner to our stakeholder Hitachi Zosen Corporation. The Kanadevia Inova commitment encourages us in our daily business and makes us a reliable partner in all kinds of situations.
Code of Conduct
Kanadevia Inova will not tolerate discrimination, conflicts of interest, bribery and corruption, insider trading, political contributions or non-compliance with the law. Kanadevia Inova and its employees respect the rules of fair competition and intellectual property rights. The business assets of Kanadevia Inova are used carefully and protected in accordance with good business practice.
Health, Safety and the Environment
Kanadevia Inova’s strategic and operational HSE focus is on providing a safe and healthy working environment for all our employees and partners. Kanadevia Inova respects the natural environment and we work to minimise our negative
impact on it and our use of natural resources wherever possible. Built around our value of actively caring for our people and the environment, and coupled with our aim of zero incidents, our strategy is based on
three core principles: competence, compliance and community. Our HSE strategy, policies and procedures provide orientation, but it is our actions that demonstrate how we actively care for all our employees and partners,
ensuring that they return home safely to their families every day.